Why should every small workshop/garage have to have a press drill?
Discover the key reasons why a drill press is an essential tool for any small workshop or garage. This blog explores the differences between drill presses and hand drills, shares expert insights, and provides a step-by-step account of upgrading a budget-friendly drill press into a near-professional machine. Perfect for hobbyists and DIY enthusiasts looking to enhance their precision and efficiency in tackling tough materials.
John Smith
8/14/20244 min read
What is the main difference between a press drill and a hand drill (cord or cordless, doesn’t matter)? The main difference is that you bring a workpiece to the press drill, in the opposite case you bring the hand drill to the workpiece. Seem to be hard? If you want a bigger precession, or you want to do drilling on the harder materials (such as steel parts), you have to believe me, it is not harder. Considering me, maybe I am not relevant because I am a hobby user, let’s see what the experts say.
The largest amount of advice, from machine user experts you can find on the forum Practical Machinist. I found a thread with a similar question and here are some expert answers:
“Definitely useful.
Mostly I use the DP for the second operation chamfering on turned or cnc milled parts. If you don't have a mill with a quill and a big enough table to spindle distance, a drill press is necessary. Spot the hole locations on the mill, and move the workpiece to DP for drilling/tapping, etc.
If you have a mill with quill and proper clearance from the table, a DP is much less needed. But occasionally comes the need to quickly punch a hole into something, and your mill might be tied up for something else, or the work to be done is a rough or odd shape, so you don't want to abuse the mill.
If I were looking for a drill press for a precision shop, I'd look for a quality geared head tabletop model. Morse taper #2 or #3. The spindle speeds should be low enough for tapping/chamfering (~100ish rpm) and high enough for small drills. (~3000ish rpm). If you do a lot of tiny hole drilling, there are dedicated high-speed precision drill presses available.
“My small shop has 4 dps, A tiny craftsman, and holes 1/8 or smaller. small countersinks. Tabletop Delta, has had a 3/4" 82* countersink in it for years. Floor model Wilton, general drilling, Wilton Strands 12-speed gear head with power feed. #3 Morse taper. It has a Jacobs 1" chuck in it most of the time, I have a big Tapmatic tapping head for it and a Sunnen hone with suds for honing small engine cylinders. A week does not go by without using most of them.”
After reading the forum, and comments I have decided to get one press drill with MT#2. Occasionally those with MT#2 drill holes up to 13 mm, in 2 passes minimum. The next question after I decided on press drill size was the manufacturer. Looking over the Internet, there is a large offer for those press drills. Their price range goes from $200 to $600 depending on the manufacturer. Those prices are for hobby variants. What was a bit odd for me, all of those hobby variants were made for the single-phase current, and almost all of them with poor switches.
I personally like the 3 phase current and massive switch with which you do not need to worry how many times you turned it on. So I decided to conduct the experiment. The experiment was about purchasing a used press drill and inserting a 3-phase motor with same the characteristics as the single phase it was on it (power, RPM). And inserting of that motor also required a new current switch. The second goal was not to exceed the price of the cheapest one with the same characteristics.
I have started looking at the local market of the used machines. After a couple of days of looking, I found one Einhell TB-13/5E. I went to the seller and checked its condition (it was selling for $70, which was odd). The switch on it was broken, but everything else was in really good condition. That doesn’t matter to me, because I already decided to exchange the driving motor and insert a new switch. I brought the Einhell press drill to my garage and went with a deep check of its condition. I also used a 3-phase motor which suits the needs of my press drill (by the way 3-phase motor was more expensive than a press drill). I made some adjustments and exchanged everything as I imagined previously.
Take a look at the introduction picture of this blog. The press drill in the picture is the drill in which the story was described. With those small enhancements, I went from a hobby variant to an almost semi-pro variant of bench top press drill. If you have time after reading this blog post, take a look at the YouTube channel to see that press drill in action. In the past couple of weeks, I have been doing shelves for the home décor and wall décor, so the press drill become an essential tool for most of my hobby products.
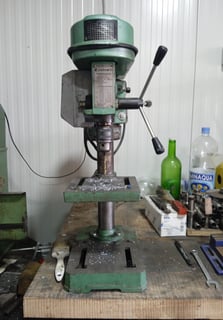
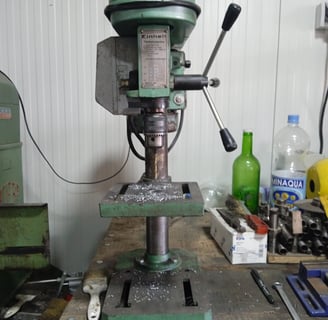
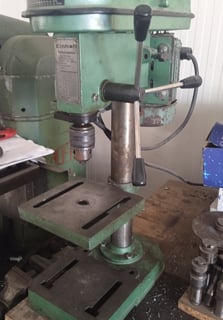
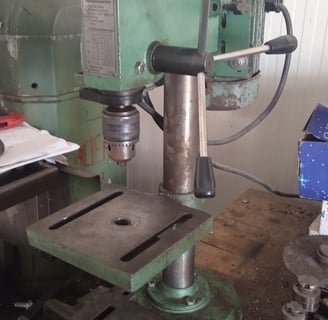
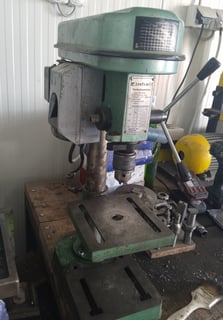
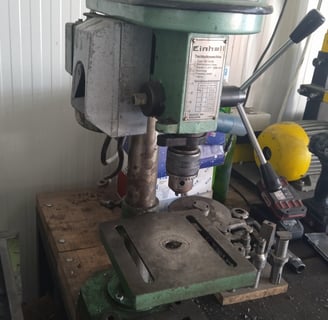